In today’s rapidly developing industrial field, hollow boards are widely used as an important material in fields such as construction, packaging, and transportation. The PP hollow board production line equipment is a key tool for producing this high-quality hollow board.
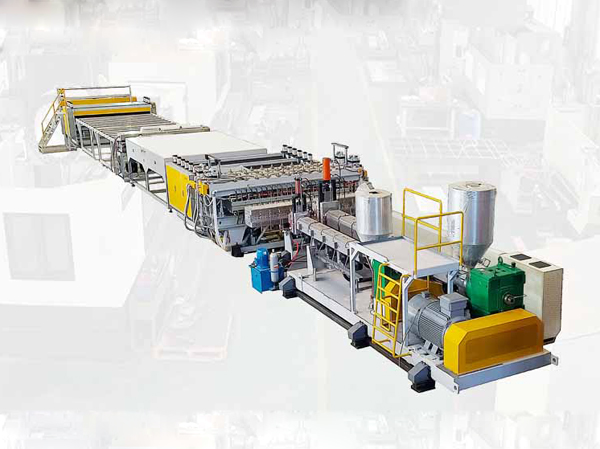
Manufacturer of automatic hollow board production line
Hollow board pulling machine, commonly known as hollow board production line equipment, is mainly used for producing PP hollow grid board and plastic hollow board (Wantong board). It is a new type of material made from polypropylene (PP) or polyethylene (PE) and polylactic acid (PLA degradable) as the main raw materials, which are extruded and formed. It has the characteristics of light weight (hollow structure) and rich color. At the same time, plastic hollow boards and their products can be recycled, cleaned, and reused. As a new type of green material, it is an ideal substitute for cardboard, wooden boards, and aluminum plates in many fields. It can also be used for advertising boards, cooling rain boards, templates, partition boards, etc. Its performance is superior to that of calcium plastic corrugated boards produced by traditional rolling and hot bonding methods, and it has good economic benefits.
Basic working principle of hollow board production line
Hollow board production line is an automated production line mainly composed of raw material processing system, forming system, cooling system, cutting system, and packaging system. Its basic working principle is to produce hollow board products that meet the requirements through a series of process flows, including heating, forming, cooling, cutting, and other steps of raw materials. The hollow board production line has a high degree of automation, high production efficiency, stable product quality, and is suitable for large-scale production and customized production.
Main components of hollow board production line
The hollow board production line equipment consists of multiple main components, each of which plays an important role in ensuring the normal operation of the production line and the manufacturing of high-quality hollow board products. Here are introductions to several of the main components:
- Extruder: The extruder is one of the most critical parts of the entire production line equipment. It melts polypropylene particles into a molten state through heating and pressure, and extrudes them into continuous hollow plates. The design and performance of the extruder directly affect the quality and production efficiency of the hollow board.
- Molding mold: Molding mold is a key component used for shaping and forming hollow boards. Its shape and structure determine the thickness, size, and surface quality of the hollow board. Molding molds are usually made of high-strength and wear-resistant materials to ensure long-term stable operation and high-precision molding effects.
- Cooling system: The cooling system plays an important role in production line equipment. It controls the temperature and flow rate of the cooling medium to quickly cool the molten polypropylene and solidify it into stable hollow board products. The design and regulation capability of the cooling system are directly related to the quality and production efficiency of the hollow board.
- Cutting equipment: The cutting equipment is used to cut the cooled and solidified hollow board into the required length and width. Cutting equipment usually uses high-speed rotating cutting tools or cutting mechanisms, which can quickly and accurately complete cutting operations to meet the production of hollow boards with different size requirements.
- Plastic surgery equipment: Plastic surgery equipment is used to trim the edges of hollow boards, giving them a flat and beautiful appearance. Through cutting, bending, polishing and other processes, shaping equipment can finely process and trim hollow boards to meet customers’ appearance and functional requirements.
- Storage and transportation system: The storage and transportation system is responsible for storing and transporting the produced hollow board products. The storage area needs to have suitable temperature, humidity, and ventilation conditions to ensure the quality and stability of the hollow board products. The conveying system can transport hollow board products from the production line to the storage area, and classify and stack them.
The various components of the hollow board production line equipment work closely together to ensure the smooth progress of the entire production process and the manufacturing of high-quality hollow board products.
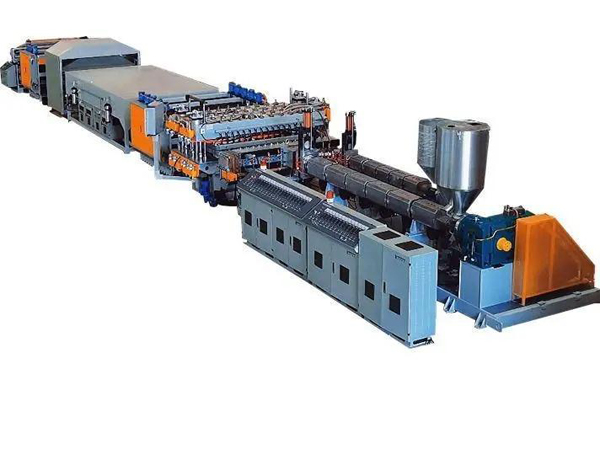
Working principle of hollow board production line
The hollow board production line equipment adopts advanced production processes and technologies, which can efficiently manufacture high-quality hollow board products. Its main working principle can be divided into the following steps:
- Raw material preparation: The main raw material for PP hollow boards is polypropylene (PP) resin particles. In the production line equipment, it is necessary to first preprocess these raw materials, including drying, mixing, heating, and other processes, to ensure the quality and plasticity of the raw materials.
- Extrusion molding: After the raw materials are prepared, the pre treated polypropylene particles are sent into the extruder. The extruder melts polypropylene into a molten state through the action of heating and pressure. Then, the molten polypropylene is passed through the die of the extruder to form continuous hollow sheets.
- Molding and cooling: After passing through the extruder, the hollow plate enters the molding section. In the molding part, by adjusting the shape and structure of the molding mold, the hollow plate can be formed to the required thickness and size. Meanwhile, through the cooling system, the molten polypropylene is rapidly cooled to solidify into stable hollow board products.
- Cutting and shaping: After cooling and solidification, the hollow board product enters the cutting and shaping stage. Cut the hollow board into the required length and width using professional cutting equipment. Then, using shaping equipment, the edges of the hollow board are trimmed to give it a flat and aesthetically pleasing appearance.
- Storage and packaging: Finally, the produced hollow board products will be sent to the storage area and packaged. In the storage area, hollow board products need to be properly stacked and classified to ensure product quality and ease of management. The packaging process involves packaging the hollow board to protect the safety and integrity of the product during transportation and use.
The hollow board production line equipment has the following advantages:
- Efficient production: The hollow board production line equipment adopts an automated control system, which can achieve automation and continuity of the production process, greatly improving production efficiency.
- Stable quality: The hollow board production line equipment has a precise control system that can monitor and adjust the parameters during the production process in real time, ensuring the stable quality of the product.
- Time and effort saving: The hollow board production line equipment adopts automated operation, reducing the time and labor intensity of manual operation and improving production efficiency.
- Environmental protection and energy conservation: The hollow board production line equipment adopts efficient energy utilization and waste disposal technologies, reducing energy consumption and environmental pollution.
- Multifunctionality: The hollow board production line equipment can produce hollow boards of different specifications and materials according to different needs and requirements, with strong adaptability and flexibility.