Dây chuyền sản xuất xi măng hoàn toàn tự động là dây chuyền sản xuất bao gồm một loạt các thiết bị. Nó chủ yếu bao gồm các quá trình nghiền và đồng nhất hóa trước, chuẩn bị nguyên liệu thô, phân hủy trước nhiệt, đốt clinker xi măng, nghiền xi măng và đóng gói, v.v.
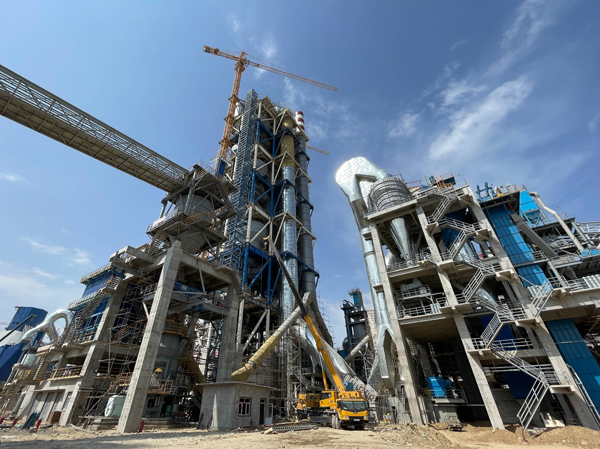
Nhà sản xuất dây chuyền sản xuất xi măng tự động hoàn toàn
Trong quá trình sản xuất dây chuyền sản xuất xi măng, mỗi 1 tấn xi măng Portland được sản xuất, cần ít nhất 3 tấn nguyên liệu (bao gồm nhiều loại nguyên liệu thô, nhiên liệu, clinker, hỗn hợp, thạch cao). Theo thống kê, việc sử dụng điện cho hoạt động nghiền của dây chuyền sản xuất xi măng khô chiếm hơn 60% tổng lượng điện tiêu thụ của toàn bộ nhà máy, trong đó nghiền nguyên liệu chiếm hơn 30%, nghiền than chiếm khoảng 3% và nghiền xi măng chiếm khoảng 40%. Do đó, việc lựa chọn hợp lý thiết bị mài và quy trình công nghệ, tối ưu hóa các thông số công nghệ, vận hành chính xác và kiểm soát hệ điều hành là rất quan trọng để đảm bảo chất lượng sản phẩm và giảm tiêu thụ năng lượng.
Phương pháp xử lý công nghệ để sản xuất xi măng
Quy trình sản xuất xi măng Portland là đại diện cho thiết bị sản xuất xi măng. Nó chủ yếu sử dụng đá vôi và đất sét làm nguyên liệu thô, được nghiền nát, tỷ lệ và nghiền thành nguyên liệu thô. Sau đó, chúng được cho vào lò xi măng cho các vật liệu trưởng thành calcine, và Clinker được nghiền mịn với một lượng thạch cao thích hợp (đôi khi được trộn với các vật liệu khác hoặc các chất phụ gia).
Thiết bị sản xuất xi măng có thể được chia thành hai loại tùy thuộc vào phương pháp chuẩn bị nguyên liệu: dây chuyền sản xuất xi măng khô (bao gồm các phương pháp bán khô) và dây chuyền sản xuất xi măng ướt (bao gồm cả phương pháp bán ẩm).
Xem xét quy trình sản xuất xi măng. Phương pháp đồng thời sấy và nghiền nguyên liệu thô, hoặc đầu tiên sấy và nghiền chúng thành bột nguyên liệu, và sau đó cho chúng vào một lò khô để ủ vào clinker. Nhưng cũng có một phương pháp thêm một lượng nước thích hợp vào bột nguyên liệu để tạo ra quả cầu nguyên liệu thô, sau đó được gửi đến lò Libol để ủ vào clinker, được gọi là phương pháp bán khô, mà vẫn là một trong những phương pháp sản xuất khô.
Tiến trình sản xuất xi măng ướt. Phương pháp nghiền nguyên liệu thô thành bùn bằng cách thêm bột nước và cho chúng vào lò nung ướt cho vật liệu trưởng thành calcine. Ngoài ra còn có một phương pháp khử nước bùn nguyên liệu được điều chế bằng phương pháp ướt, làm cho các khối nguyên liệu thô và làm nóng vật liệu trưởng thành trong lò nung, được gọi là phương pháp semi Wet, mà vẫn là một trong những phương pháp sản xuất ướt.
Ưu điểm chính của sản xuất khô là tiêu thụ nhiệt thấp (ví dụ, tiêu thụ nhiệt của clinker trong lò khô với vòi phun tiền là 3140-3768 coke/kg), nhưng bất lợi là thành phần nguyên liệu thô không dễ thống nhất, xưởng có khí thải bụi cao và tiêu thụ điện cao. Sản xuất ướt có lợi thế là vận hành đơn giản, kiểm soát dễ dàng thành phần nguyên liệu thô, chất lượng sản phẩm tốt, vận chuyển bùn thuận tiện và ít bụi hơn trong xưởng. Sự bất lợi là tiêu thụ nhiệt cao (clinker heat tiêu thụ thường là 5234-6490 coke/kg).
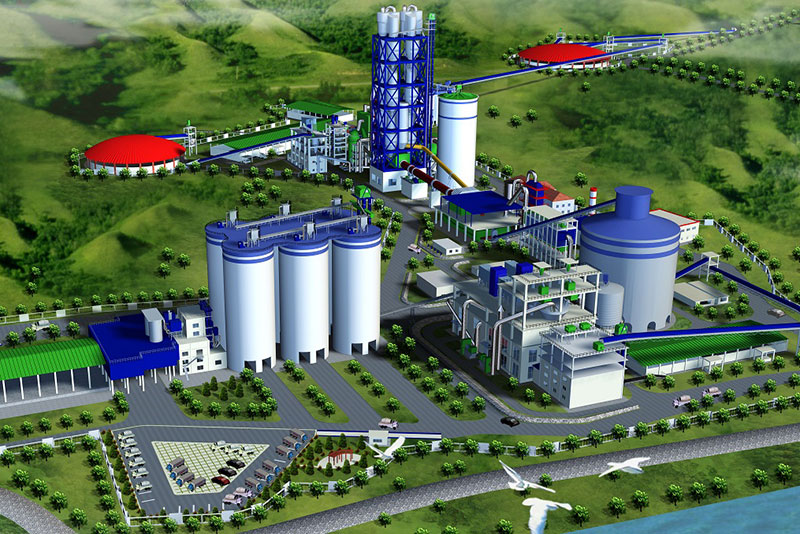
Quy trình của dây chuyền sản xuất xi măng quy trình khô mới:
Sự phân hủy trước khi nung nóng
Tiền nhiệt và phân hủy một phần của vật liệu thô được hoàn thành bởi các bộ tiền nhiệt, thay thế một số chức năng của các lò quay, để rút ngắn chiều dài của lò. Đồng thời, quá trình trao đổi nhiệt vật liệu khí trong lò được thực hiện ở trạng thái xếp chồng và chuyển đến trạng thái lơ đễn. Prenung, cho phép nguyên liệu thô trộn hoàn toàn với khí thải ra từ lò, tăng diện tích tiếp xúc vật liệu khí, tốc độ truyền nhiệt nhanh, hiệu quả trao đổi nhiệt cao và đạt được mục tiêu cải thiện hiệu quả sản xuất của hệ thống lò và giảm tiêu thụ nhiệt của clinker đốt.
Nghiền nát và trước đồng nhất
1) Nghiền nát: Trong quá trình sản xuất xi măng, phần lớn nguyên liệu cần phải được nghiền nát, như đá vôi, đất sét, quặng sắt và than đá. Đá vôi là nguyên liệu thô được sử dụng trong sản xuất xi măng, với kích thước hạt lớn hơn và độ cứng cao hơn sau khi khai thác. Vì vậy, việc nghiền đá vôi đóng một vai trò quan trọng trong việc nghiền vật liệu ở các cây xi măng.
(2) Tiền đồng nhất hóa vật liệu thô: Công nghệ tiền đồng nhất là sử dụng các kỹ thuật xếp chồng và thu hồi khoa học trong quá trình lưu trữ và thu hồi vật liệu thô để đạt được đồng nhất sơ bộ của nguyên liệu, cho phép sân vật liệu thô có cả chức năng lưu trữ và đồng nhất.
Nguyên liệu chuẩn bị
Trong quá trình sản xuất xi măng, mỗi tấn xi măng Portland được sản xuất, ít nhất 3 tấn vật liệu (bao gồm các nguyên liệu khác nhau, nhiên liệu, clinker, hỗn hợp và thạch cao) cần phải được nghiền nát. Theo số liệu thống kê, mức tiêu thụ năng lượng của hoạt động nghiền xi măng khô chiếm hơn 60% tổng tiêu thụ điện của nhà máy, trong đó nguyên liệu nghiền chiếm hơn 30%, than nghiền chiếm khoảng 3%, và nghiền xi măng chiếm khoảng 40%. Do đó, lựa chọn hợp lý các thiết bị xay và luồng quy trình, tối ưu hóa các thông số quy trình, vận hành chính xác và kiểm soát hệ điều hành có ý nghĩa lớn để đảm bảo chất lượng sản phẩm và giảm tiêu thụ năng lượng.
Nguyên liệu đồng nhất hóa
Trong quá trình sản xuất xi măng khô mới, ổn định thành phần của nguyên liệu thô vào hố là một điều kiện tiên quyết để ổn định hệ thống nhiệt của đốt clinker, và hệ thống đồng nhất hóa vật liệu thô đóng một vai trò quan trọng trong việc ổn định thành phần của nguyên liệu thô vào hố.
(1) Tính chất phân tán
80% sự trao đổi nhiệt xảy ra trong đường ống inlet. Nguyên liệu được đưa vào đường ống preheater bị lệch hướng lên bởi luồng không khí tăng tốc độ cao và bị phân tán.
(2) Tách khí cứng
Khi dòng không khí mang bột vào xoáy thuận, nó buộc phải xoay và chảy trong không gian hình khuyên giữa vật xoáy và xi lanh bên trong (ống xả), và di chuyển xuống trong khi quay, từ xi lanh đến hình nón, mở rộng tất cả các cách đến cuối hình nón, và sau đó quay lên để được xả qua các ống xả.
(3) Phân hủy
Sự xuất hiện của công nghệ tiền phân hủy là một bước nhảy vọt công nghệ trong quá trình calcination xi măng. Nó liên quan đến việc thêm lò phân hủy giữa prenung và lò nung quay, sử dụng khói đuôi lò nung tăng lên, và lắp đặt một thiết bị phun nhiên liệu để cho phép quá trình tỏa nhiệt của quá trình đốt nhiên liệu và quá trình nhiệt độ phân hủy cacbonat của vật liệu thô nhanh chóng xảy ra trong trạng thái lơ lửng hoặc lỏng bên trong lò phân hủy, do đó làm tăng tốc độ phân hủy của vật liệu thô vào lò trên 90%. Chuyển nhiệm vụ phân hủy cacbonat ban đầu được thực hiện trong lò quay đến lò phân hủy; Hầu hết nhiên liệu được thêm vào từ lò phân hủy, với một lượng nhỏ được thêm vào từ đầu lò, làm giảm tải nhiệt trên vùng nung bên trong lò, kéo dài tuổi thọ của vật liệu lót, và có lợi cho sản xuất quy mô lớn; Do sự trộn đồng nhất của nhiên liệu và nguyên liệu thô, nhiệt đốt của nhiên liệu nhanh chóng được chuyển giao cho vật liệu, tối ưu hóa quá trình đốt, trao đổi nhiệt và các quá trình phân hủy cacbonat. Do đó, nó có một loạt các hiệu suất và đặc điểm tuyệt vời như chất lượng cao, hiệu quả cao và tiêu thụ thấp.
Bao bì bằng xi măng
Xi măng có thể được vận chuyển theo hai cách: bagged và bulk.
Đang đốt xi măng clinker
Sau khi nguyên liệu thô được làm nóng trước và bị phân hủy trong bộ phận điều chế Cyclone, quá trình tiếp theo là để vào lò quay để đốt Clinker.
Trong lò nung quay, cacbonat tiếp tục phân hủy nhanh chóng và trải qua một loạt các phản ứng ở pha rắn, sản xuất các khoáng chất như khoáng chất trong xi măng Clinker. Khi nhiệt độ của vật liệu tăng lên, các khoáng chất sẽ biến đổi thành một pha lỏng, và những chất hòa tan trong pha lỏng sẽ phản ứng để tạo ra một lượng lớn Clinker. Sau khi clinker bị đốt, nhiệt độ bắt đầu giảm. Các clinker nhiệt độ cao thải ra từ lò quay được làm mát bởi một clinker xi măng làm mát đến nhiệt độ mà giao thông xuôi dòng, lưu trữ và các nhà máy xi măng có thể chịu được. Đồng thời, nhiệt độ hợp lý của clinker nhiệt độ cao được phục hồi để cải thiện hiệu suất nhiệt và chất lượng Clinker của hệ thống.
Xay xi măng
Luyện xi măng là một quá trình trong sản xuất xi măng tiêu thụ nhiều điện. Chức năng chính của nó là nghiền xi măng Clinker (cũng như các chất kết tủa, điều chỉnh hiệu suất vật liệu, vv) với kích thước hạt thích hợp (thể hiện trong độ mịn, diện tích bề mặt cụ thể, vv), tạo thành một phân phối kích thước hạt nhất định, tăng diện tích hydrat hóa của nó, tăng tốc tỷ lệ hydrat hóa và đáp ứng các yêu cầu của thiết lập xi măng và cứng.
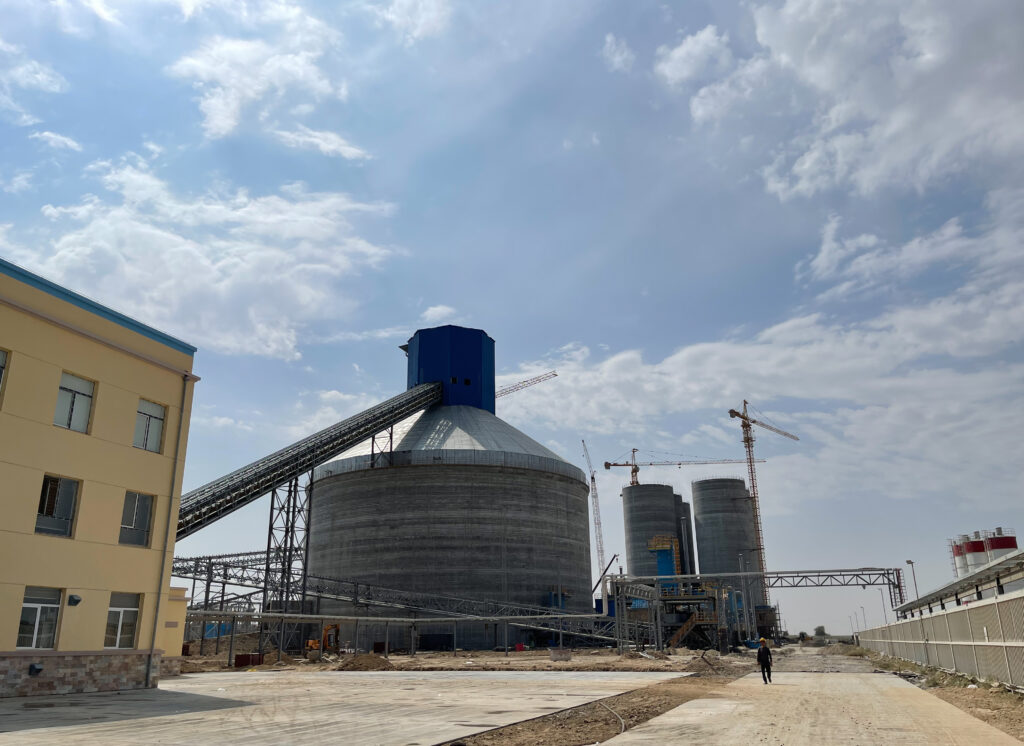
Ưu điểm nổi bật của dây chuyền sản xuất xi măng
Sản lượng lớn, chất lượng tuyệt vời, hoạt động tổng thể êm hơn, và tỷ lệ thất bại tương đối thấp, giảm chi phí bảo trì hơn 150000 nhân dân tệ mỗi năm;
Thiết kế thân thiện với môi trường mang tính khoa học hơn và giải quyết đầy đủ vấn đề ô nhiễm của dây chuyền sản xuất truyền thống, tạo ra một nơi sản xuất xanh lý tưởng;
Chất lượng xi măng clinker được sản xuất là tuyệt vời, với giá trị ứng dụng công nghiệp tăng lên 1, 5 lần, có thể thu hút nhiều sự chú ý của người dùng hơn và có giá thị trường cao hơn;
Khả năng tiết kiệm năng lượng tuyệt vời và tiêu thụ than thấp, có thể tiết kiệm cho doanh nghiệp ít nhất 200000 nhân dân tệ theo chi phí hàng năm;
Hệ điều hành tự động yêu cầu nhân viên tại chỗ tối thiểu, an toàn và hiệu quả, và giảm chi phí lao động khoảng 80%;
Diện tích đất tổng thể của dây chuyền sản xuất đã được giảm 1/4, điều này đã giảm giới hạn địa điểm và tiết kiệm chi phí cơ sở hạ tầng cho doanh nghiệp 300000 nhân dân tệ.
Chúng tôi có thể cung cấp nghiên cứu khả thi, thiết kế, ký kết hợp đồng chung, vận hành sản xuất và các dịch vụ khác cho dây chuyền sản xuất xi măng với số lượng hàng ngày lên tới 500-10000 tấn với các thông số kỹ thuật khác nhau.
Tổng sản lượng hàng ngày là 10000 tấn
Sản lượng hàng ngày 5.000 tấn
Sản lượng hàng ngày là 4000 tấn
Sản lượng hàng ngày là 2500 tấn
Sản lượng hàng ngày là 500 tấn
Tùy biến theo nhu cầu